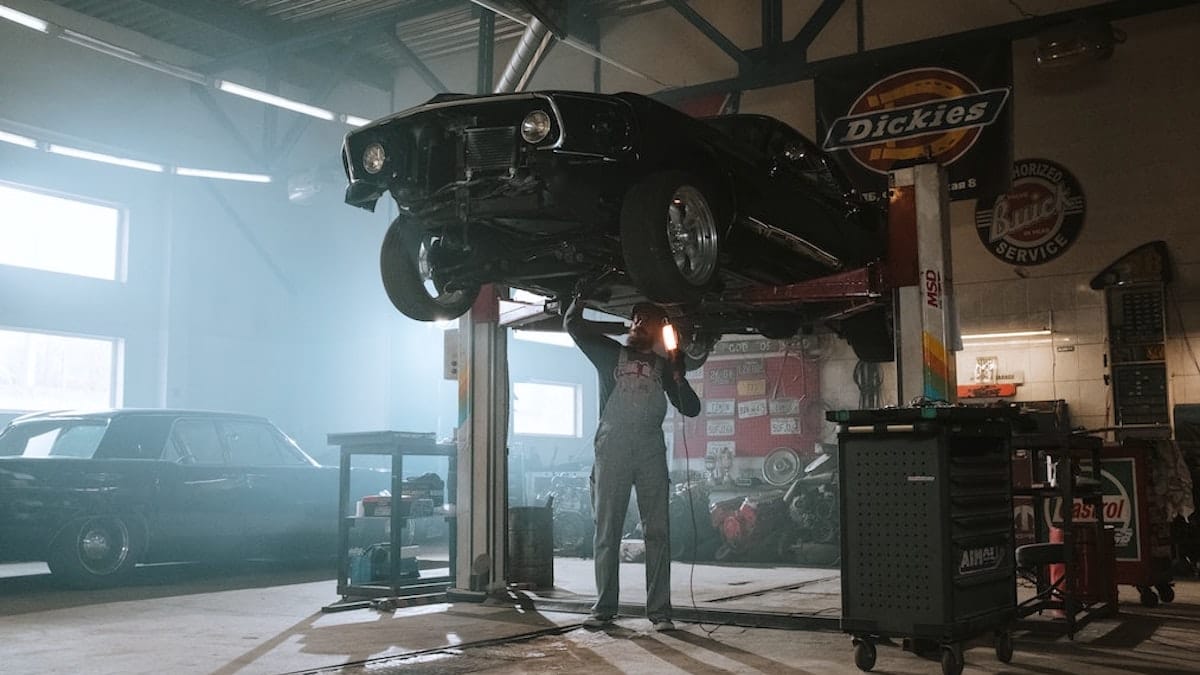
As clean transportation tech moves forward, is the human side ready?
Reading Time: 3 minutes Over the next five years, US public agencies will spend billions to clean up the transportation sector. A large share of that money is earmarked for training blue-collar workers in disadvantaged communities on the specific tasks of sustaining a zero-emission economy. While th
Over the next five years, US public agencies will spend billions to clean up the transportation sector. A large share of that money is earmarked for training blue-collar workers in disadvantaged communities on the specific tasks of sustaining a zero-emission economy. While the need for worker training is obvious, the specifics of who and how have been elusive. As the looming rail strikes remind us, the specifics of how industry and government support laborers in the freight sector is critical to economic success.
Working-class livelihoods are deeply intertwined with fossil fuels. Today, as the American wealth gap expands and the need to replace petroleum with renewables becomes more urgent, the laborers who build, operate, and maintain the equipment moving the US economy risk being left behind.
Training on uncertainty
Part of the challenge is that the clean vehicle ecosystem lacks mature technologies and standards on which workers can be trained. Charging depots need to be built and maintenance shops need to stock up—but who is qualified and what tools are needed? Uncertainty reaches further down the supply chain. What does a fire marshal need to know about hydrogen to approve a new fueling station?
These nuts-and-bolts questions have generally gone unanswered while clean tech figured if and how to build clean vehicles. But in the last 18 months, the first commercial battery and hydrogen fuel cell trucks were proven on public roads, and in 2023, US contractors are due to break ground on a massive amount of electric and hydrogen infrastructure to support them. Yet they face an extreme shortage of qualified workers. Answers to the who and how of workforce development are needed.
This year, the first responses emerged.
First movers set examples
Refuse truck manufacturer Mack Trucks launched a program to certify dealerships and technicians to support its electric refuse truck—and supporting charging equipment—in multiple regional markets. Volvo Trucks North America completed a partnership with community and technical schools in Southern California to train technicians and help first responders develop public training resources, now available from the National Fire Protection Agency. In Detroit, MI, Daimler Trucks North America expanded its training center to accommodate EV-specific technical training programs.
These are important first examples of what workforce development looks like. But they have been developed by the largest players under grant-funded partnerships. Regulators and educators must pick up these tangible models and do real work to adapt and distribute these models to smaller providers nationwide—especially in areas where EVs and fuel cells still seem like a fairytale.
Programs must go farther and deeper for equitable change
Large segments of the US commercial transportation support system rely on independent operators and small business owners. This demographic is highly sensitive to economic shifts, especially in rural and disadvantaged areas where EVs are hardly an option. If a technician never sees an EV, how can they prepare to fix one? If a small town does not have a hydrogen fuel cell truck in demonstration today, how can its politicians adapt local rules and ordinances to safely allow fueling stations when commercial fleets start showing up in five years?
Lack of exposure risks making technicians and drivers in blue-collar and disadvantaged communities less competitive for emerging jobs. In addition to adapting manufacturer-specific training programs for general use, regulators and educators must help communities acclimate to and profitably participate in the new transportation system. Programs like the Electric Truck Research and Utilization Center (eTRUC) can introduce working-class communities to new technologies and position their students and workers as fluent and capable professionals.
The industrial age was built on the backs of cheapened labor, engendering a host of social ills. Building a clean energy economy is a chance to make some corrections. As the US advances its clean transportation agenda, the subject of workforce development must move past policy speak and into actionable programs that keep workers working.